Logistics
Workforce Management Software for Warehouse Staff: Empowering On-The-Go Productivity
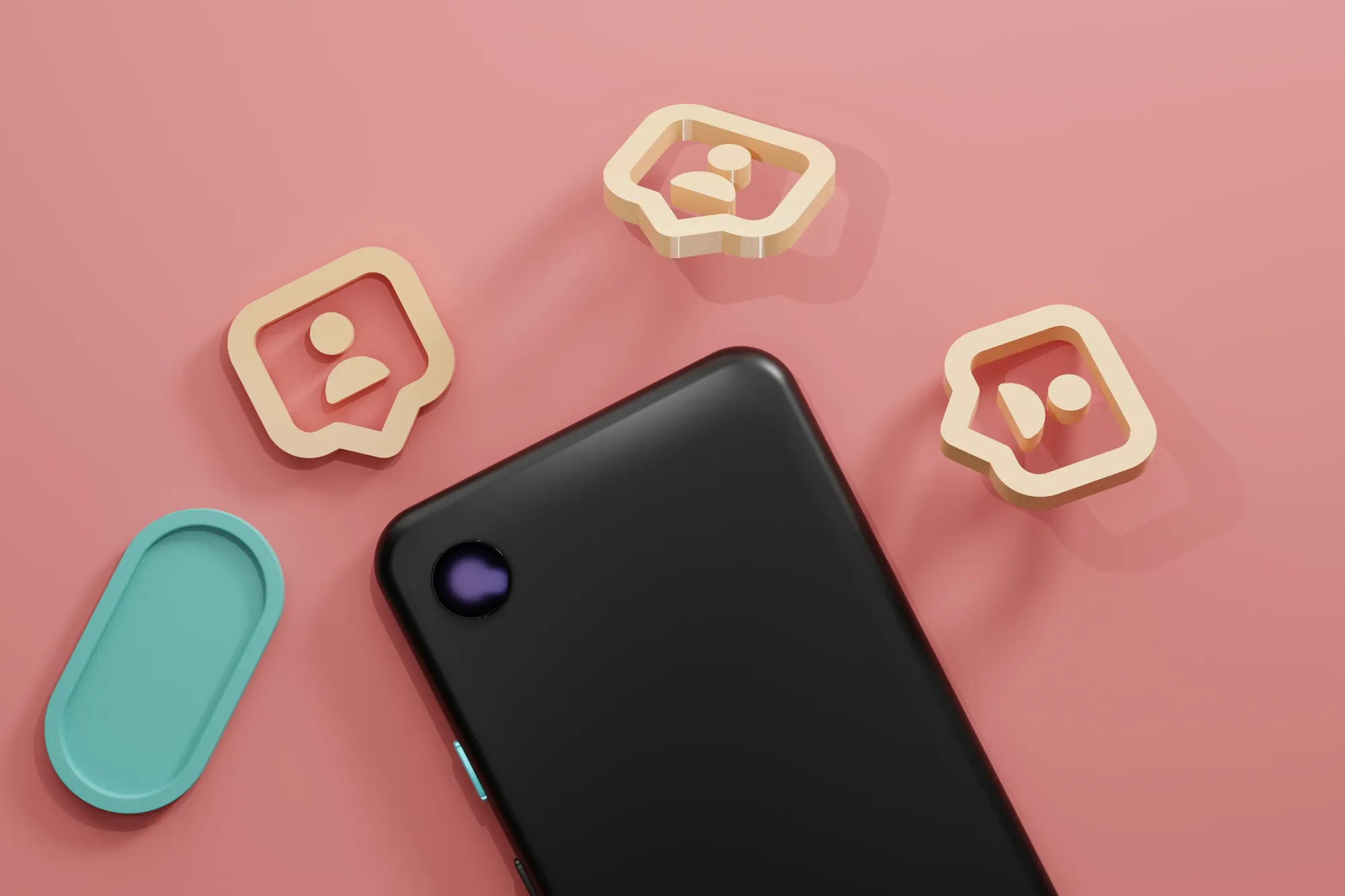
In warehousing, one fact rings louder than others: 50-70% of a warehouse's budget typically goes toward labor costs. Facing this significant expense, the industry is poised on the brink of a digital revolution driven by workforce management software.
With one touch, they streamline cumbersome processes and offer real-time data management, effectively placing control of operations into the hands of warehouse staff.
Here, we explore these transformational tools, their features, and how they effortlessly integrate into your current warehousing operations, offering a stark upgrade from traditional methods.
The Role of Workforce Management Software in Modern Warehousing
Mobile warehouse management software induces highly sought-after modern improvements such as operational efficiency, real-time data access, and superior workforce adaptation into warehouse activities.
Interestingly, findings highlight companies with fully integrated mobile warehouse management systems reporting:
- A 25% reduction in order fulfillment errors
- A decrease in employee onboarding time by an impressive 50%
- A 20% decrease in overall inventory holding costs
These sought-after improvements underscore the importance of efficient logistics workforce management, which has become increasingly crucial over the last two years. Referencing data from a report by Kane Logistics, companies now place greater emphasis on this area, with 68% considering it more important, compared to 30% two years ago. This emphasis is projected to increase further, with an expected 74% of companies considering it even more important in the coming two years.
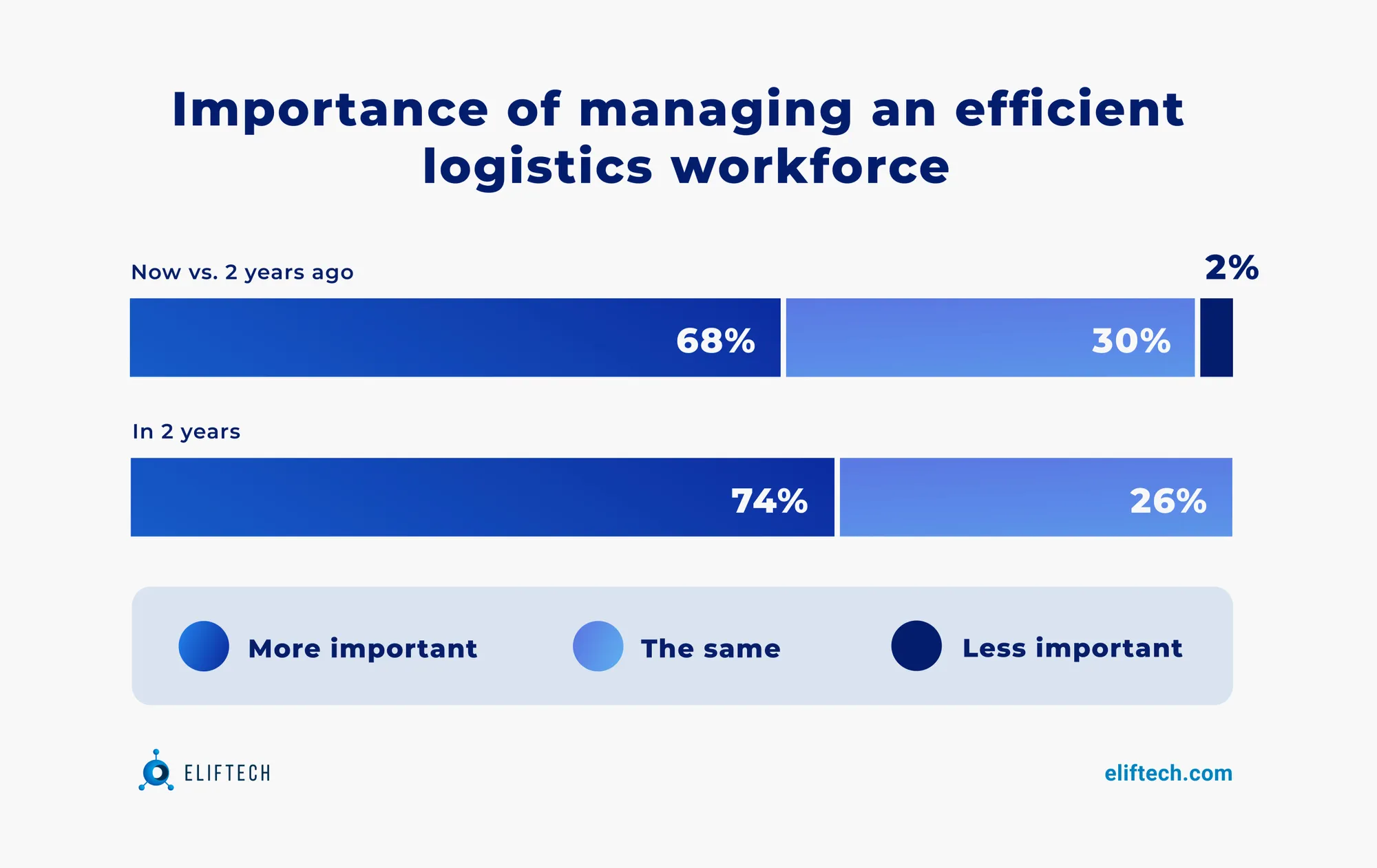
Moreover, mobile warehouse management tools have the potential to pull up the anchor that has kept warehousing operations tethered to desktop systems and traditional paper-based processes. By enabling more streamlined, mobile tasks like inventory control and shipment tracking, they signify a trend toward increased efficiency and agility.
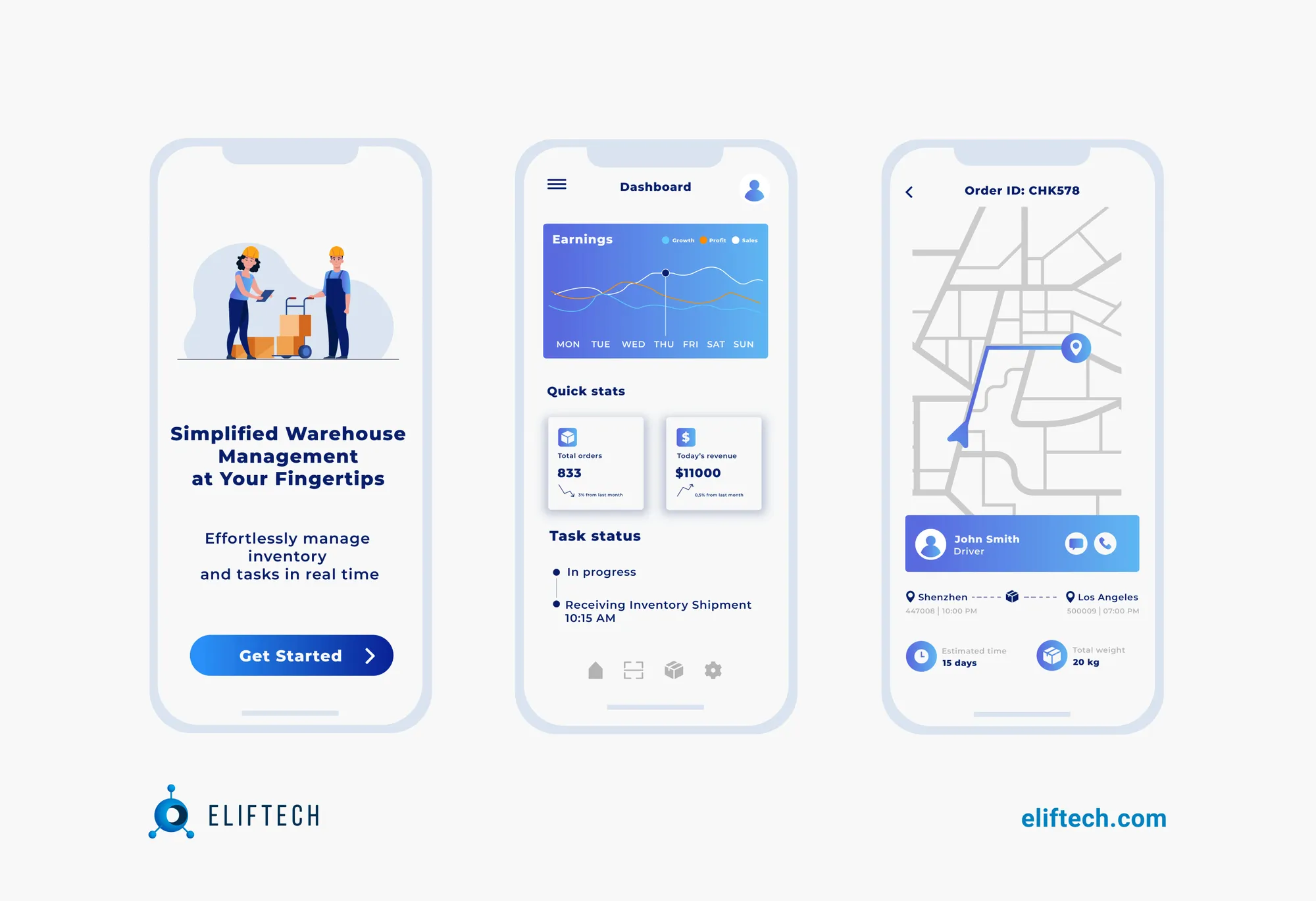
For example, take UNICEF's deployment of their mobile warehouse and inventory management solution app in their warehouses. The mobile workforce management app enables warehouse staff to record transactions digitally, significantly reducing time spent on logistics operations. The app has reduced the average time spent managing warehouse items by over 30% in 2019. In addition, third-party logistics, or 3PLs, providers could benefit from such technology breakthroughs to enhance their distribution, warehousing, and fulfillment services. This highlights the significance of digital solutions in the logistics industry.
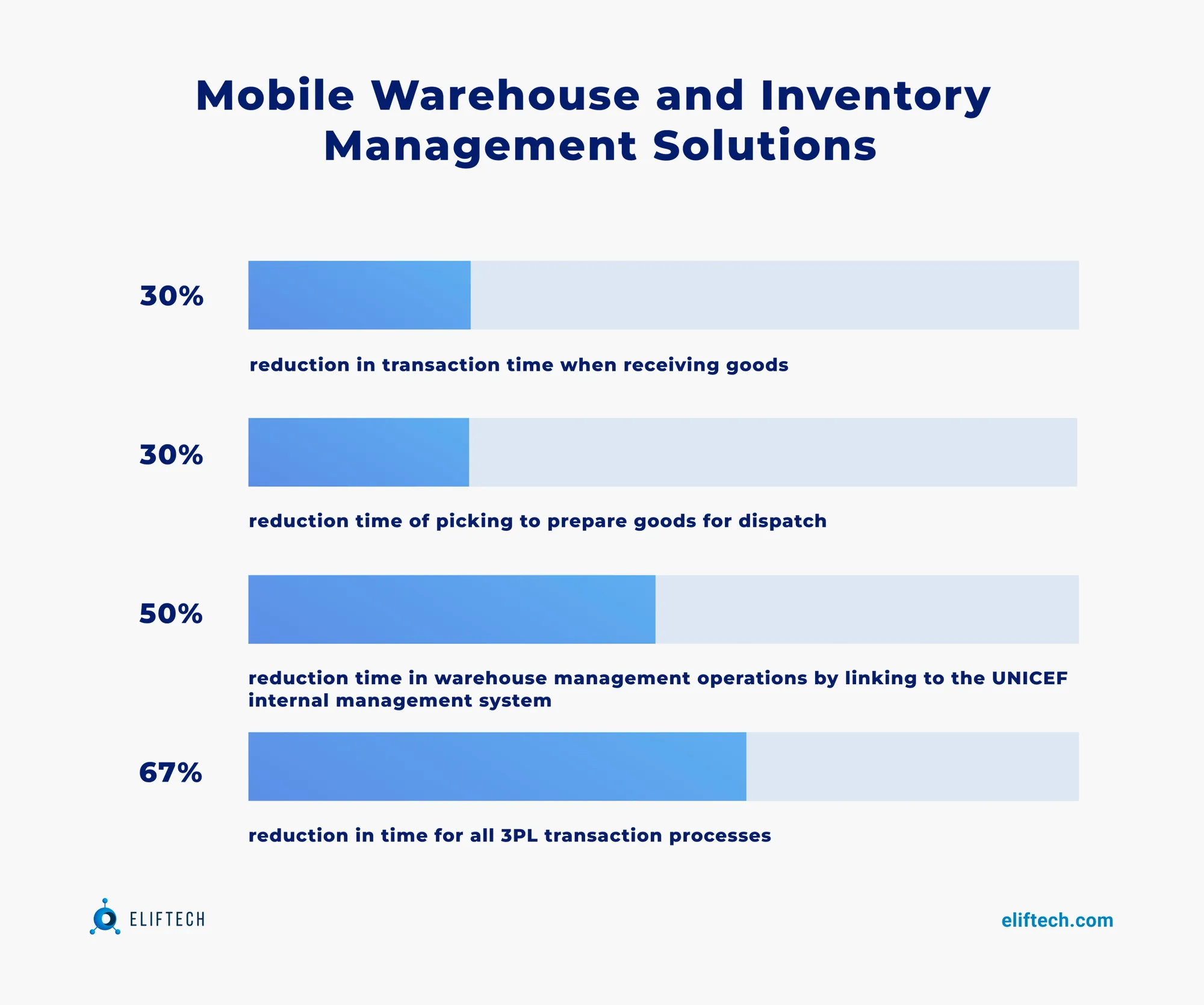
Challenges Faced by Warehouse Staff
Navigating the complex environment of a warehouse isn't devoid of challenges, often in the form of talent acquisition and retention, demand forecasting, managing inventory, overhead costs, operator utilization, efficiency, damage control, and boosting overall productivity.
According to a survey by Kane Logistics, the major challenges faced by warehouse managers comprise:
- Finding and Retaining Dependable Workers (62%)
- Increasing Workforce Productivity (57%)
- Controlling Labor Costs (45%)
Increasing Workforce Productivity
An essential aspect of warehouse operations is enhancing workforce productivity, a concern for 57% of warehouse managers. Various factors influence productivity, including the warehouse layout's efficiency, the availability and functioning of necessary tools and equipment, the effectiveness of communication, and worker motivation. The key challenge lies in identifying and implementing systems and incentives that promote these variables' optimal performance.
Labor Costs Control
Controlling labor costs is another challenge encountered by 45% of warehouse operators. These costs extend beyond salaries to encompass benefits, training, recruitment costs, and overheads such as management and human resources. The challenge lies in striking the right balance between managing these costs while fostering an efficient and motivated workforce. Strategies to mitigate this issue can involve accurate labor needs evaluation, refining recruitment processes, investing in meaningful training, and offering competitive wages to ensure staff retention.
Inefficient Inventory Management
Traditional manual inventory management can result in inefficiencies due to time-consuming paper-based processes to track stock levels, trace item locations, and manage reorder points. These methods are prone to human error, leading to inaccuracies that can impact the entire supply chain. Moreover, manual inventory drains labor hours. Businesses should consider more efficient, automated systems to improve accuracy and save on labor costs.
Beyond these, there are other challenges warehouse managers often grapple with.
Time-consuming Barcode Scanning and Label Printing
Traditional barcode scanning and label printing are manual, time-consuming processes that can lead to operational bottlenecks and inaccuracies, resulting in overall inefficiency. In the United States, manual scanning and labeling processes make up almost 20% of total warehouse operating time. Automating these processes can lead to significant time savings and improve accuracy.
Task Management and Workload Distribution
Traditional task management and workload distribution in warehouses are often subjective rather than data-driven, potentially resulting in unbalanced workloads and productivity losses. Adopting automated task management systems can significantly improve productivity by ensuring that workloads are accurately allocated based on current warehouse conditions and individual staff capacity.
Lack of Real-Time Communication
Delayed communication can cause significant latency in decision-making and operational actions. Manual updates on warehouse activities can lead to communication gaps, hindering the quick and proactive response to potential disruptions. According to typical post-project estimations, warehouses equipped with real-time communication technology can respond to unforeseen operational issues 1.5x faster than those using traditional communication channels.
Labor Management Systems and Software
As technology advances, businesses can utilize more sophisticated software and systems to manage labor, but this comes with its set of challenges. These include choosing the system that best fits the company's needs, implementing it correctly, and training staff to use it efficiently. Overcoming budget constraints, resistance to change, and the disruption caused by implementing new systems significantly contribute to this challenge. With the ever-evolving digital landscape, businesses need to stay updated with new technologies to maintain a competitive advantage.
Steer your warehouse towards enhanced, efficient operations. Learn how our technology solutions streamline processes and amplify efficiency: See ElifTech in action.
Workforce Management Software Features That Drive Productivity in Warehouses
There are certain features integrated into warehouse apps that are helping drive productivity and efficiency to unprecedented levels. Two of these paramount features are real-time tracking and data analytics. Real-time tracking allows constant monitoring of inventory and activities. In addition, automation facilitates error reduction and faster processes.
These apps offer integration with systems like warehouse ERP, and despite the varied categories - from inventory to workforce management, all aim to improve productivity.
In the following sections, we'll delve further into these features, exploring their specific functionality and impact on warehouse productivity.
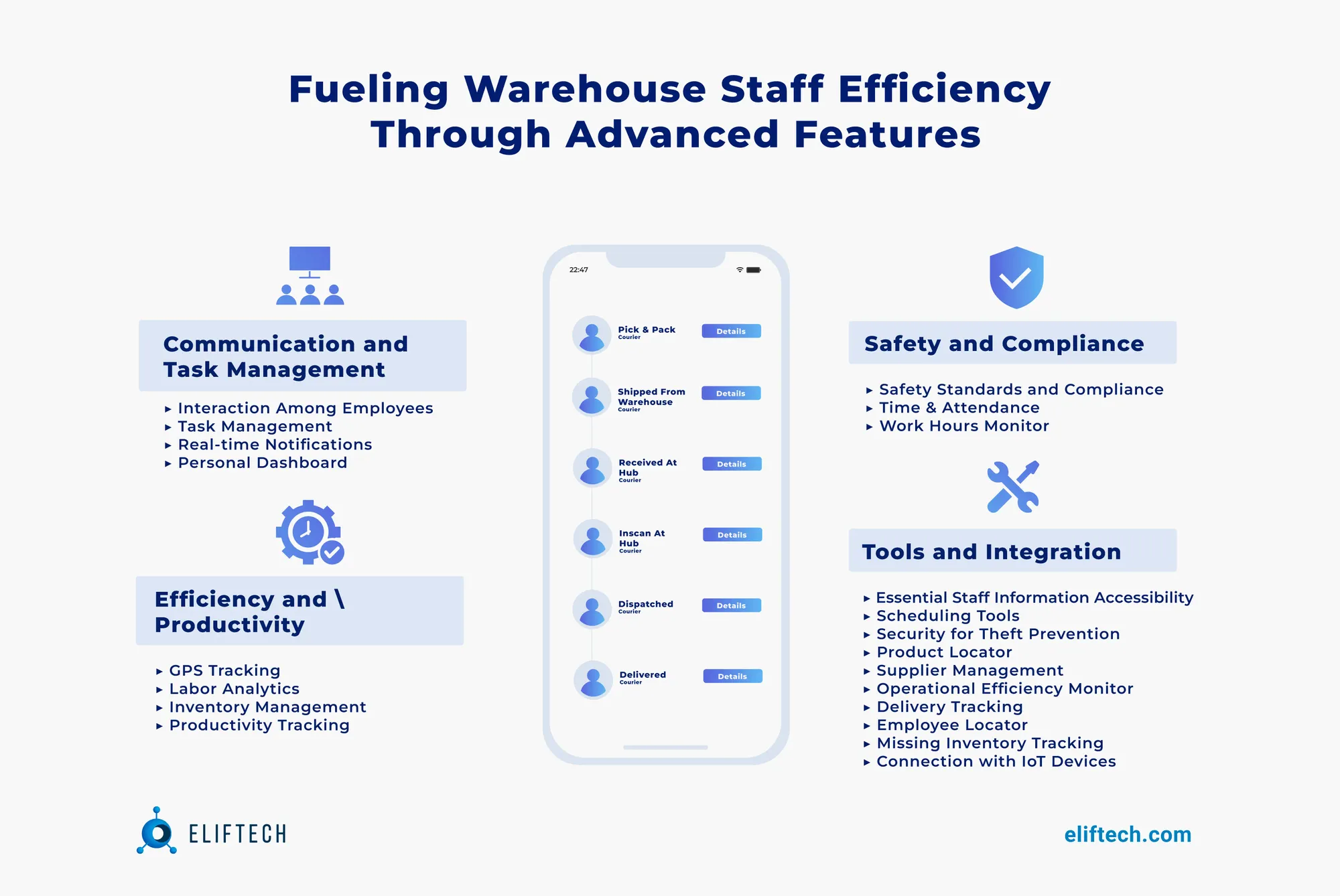
Communication and Task Management
- Collaborative Platform: Promote real-time employee interaction for rapid sharing of updates, information, and alerts.
- Task Management: Allow supervisors to assign tasks, track progress, and monitor completion status.
- Real-time Notifications: Keep employees updated about key changes or updates in work schedules.
- Personal Dashboard: Provide each employee with a dashboard to track their tasks, performance metrics, shifts, and updates.
Efficiency and Productivity
- GPS Tracking: Pinpoint the exact location of warehouse staff, which is particularly helpful in large facilities.
- Labor Analytics: Offer insights on individual and overall performance, labor cost analyses, and productivity improvements.
- Inventory Management: Maintain real-time inventory data, coordinate stock movements, and prevent discrepancies or shortages.
- Productivity Tracking: Monitor each employee's performance, output, and overall productivity levels.
Safety and Compliance
- Safety Standards and Compliance: Host safety training materials and keep employees updated about safety regulations and company policies.
- Time & Attendance: Track check-ins, breaks, and overtime, and effectively replace manual attendance tracking to ensure precise payroll management.
- Work Hours Monitor: Keep track of work hours for employees and third parties involved in warehouse operations for compliance and accurate payroll management.
Tools and Integration
- Essential Staff Information Accessibility: Retrieve essential staff information through an integrated database.
- Scheduling Tools: Cloud-based tools to create, share, and manage staff schedules remotely in a workforce scheduler app.
- Security for Theft Prevention: Integrate surveillance camera feeds and facial recognition software for improved warehouse security.
- Product Locator: Combine a barcode scanner and inventory software to locate products within the warehouse efficiently.
- Supplier Management: Maintain a list of suppliers with immediate access to contact information and inventory counts.
- Operational Efficiency Monitor: Use IoT devices for tracking and analyzing operational processes to identify strengths and weaknesses.
- Delivery Tracking: Monitor the delivery process, predict arrival and departure times, and optimize task scheduling.
- Employee Locator: Integrate geolocation tools to locate employees within the warehouse premises in real time.
- Missing Inventory Tracking: Alert and report missing items, preventing inventory discrepancies and ensuring stock level accuracy.
- Connection with IoT Devices: Track RFID-equipped items using the app to ensure accurate inventory management and help with product location in the warehouse.
How to Seamlessly Integrate a Mobile Workforce Management Software into Your Warehouse Operations
Though the process of implementing a mobile app into your warehouse may present challenges, strategic planning, training, and support can facilitate a smooth transition. The ultimate aim is to leverage app features to enhance productivity across all warehouse operations.
There are several steps to that:
Understand Your Warehouse Requirements
Understanding the specific needs of your operations is pivotal in choosing the right workforce management software. Start by conducting a thorough assessment of your current procedures, pain points, and goals. For instance, suppose your warehouse has often been dealing with misplaced stock items. In this case, a workforce management mobile app with strong inventory management and product locator features would be crucial. Similarly, if managing work hours and overtime has been troublesome, an app featuring time & attendance and work hours monitor would potentially resolve these issues. Having a clear understanding of your needs helps ensure the chosen app will effectively address your warehouse's specific challenges.
Compatibility with Existing Systems
Any new tech addition must not disrupt your existing digital setup. Ensure the mobile app can seamlessly integrate with your current WMS or IT infrastructure. If your warehouse is already using a certain program for inventory management, the new mobile app should either replace it effectively or blend with it smoothly.
In terms of hardware like scanning devices or RFID systems, your app should ideally extend their functionality, not contest with them. This compatibility increases overall operational efficiency.
User Interface & Adoption
The adoption of a new app depends heavily on its usability. The app's design should focus on user-friendliness to simplify the work, not to add complexity.
Consider an app that allows both management and staff access, providing different functions according to role permissions. The principle would be to make the transition easy and intuitive. For example, the Task Management function should enable seamless task assignment and follow-up but in a simpler, more efficient way than traditional methods.
Remember, a practical pilot run with a sample of your warehouse staff could provide valuable feedback for the training scope and highlight their doubts or resistant points. Addressing these upfront will foster a better integration process.
Optimize Your Warehouse Operations with Workforce Management Software
Embracing mobile apps in modern warehouse management paves the way for advanced productivity, reduced operational costs, and a competitive edge in an evolving industry. This transformation from traditional processes to cutting-edge digital tools significantly enhances labor management, order fulfillment, and transportation efficiency, among others.
Transforming your warehouse operations with a mobile workforce management software solution helps to:
- Refine transportation and hasten delivery and route planning
- Increase operational efficiency through automation of business processes
- Keep system tools up-to-date
- Remain competitive in today's digital era
Specifically designed for logistics, transportation, and courier companies, our mobile apps seamlessly integrate cloud and IoT technologies, offering a comprehensive solution to digitize your warehouse operations. Our apps ensure robust security, automating daily operations and staying current with the latest industry trends.
Contact us to discover how our customized logistics apps can enhance your warehouse operations.