Logistics
RPA in Supply Chain: Key Use Cases and Success Stories
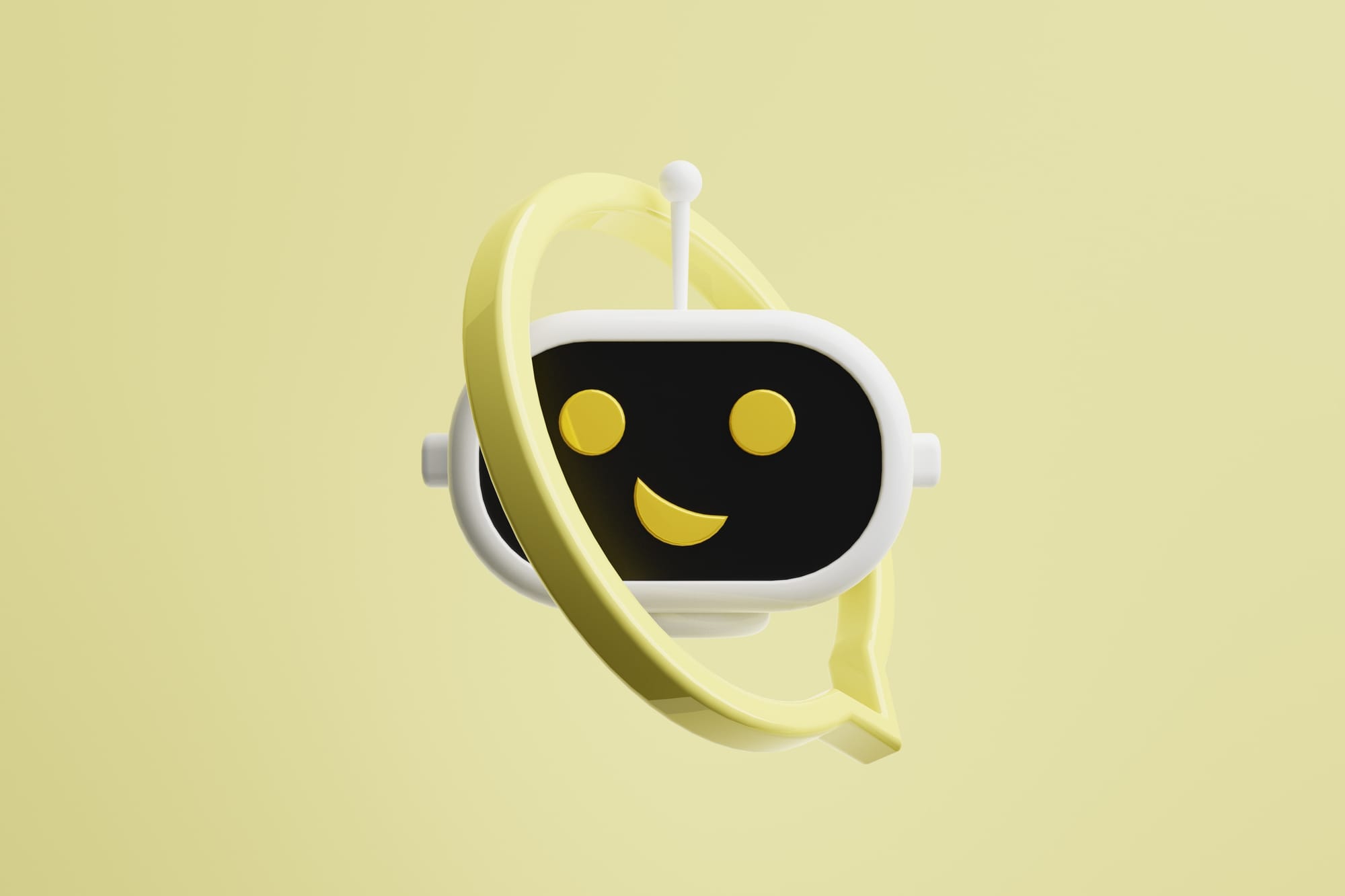
As the world speeds up, businesses feel pressured to accelerate in the logistics and supply chain industry. However, achieving this through traditional methods alone is becoming increasingly difficult. This makes implementing technologies essential to keeping up with the complexity of modern supply chain management.
Robotic process automation is one such technology. Companies are turning to RPA software to modernize their supply chain process, and they generally find it highly beneficial. But what exactly makes RPA systems so special, and why are they the best choice for improving processes in supply chain management? That’s precisely what we’ve covered in this article.
Understanding RPA and Its Role in Supply Chain Management Processes
Before going into specific RPA applications in supply chain management, we want to explain what an RPA solution is, how it works, and why it has become invaluable for modern supply chain operations.
What is RPA?
Robotic process automation (RPA) is a technology that automates repetitive tasks with the help of so-called “bots”—software applications that mimic human actions within digital systems. For example, RPA bots can extract data from emails or internal documents, input data into ERP systems, fill in forms, and generate reports. They perform most routine tasks independently, following a strict set of instructions.
Unlike traditional automated processes, which require connecting different systems and making them interact with each other, RPA interacts with systems directly in the way a human employee would.
Let’s say you need to automate inventory reports. With traditional automation, supply data for a report is pulled from WMS and ERP systems with the help of an API and processed through fixed scripts. Plus, it requires manual script updates in case of any data format changes (like a new field added).
RPA, on the other hand, will create reports by actually logging into both systems, finding and copying required information, and then compiling it into a report. If there’s a change in the data, you can easily adjust the bot’s settings through the user interface without needing assistance from the IT department.
Why is RPA critical in modern supply chain business processes?
Fictiv’s State of Manufacturing Report from 2023 found that over half of manufacturers struggle with analyzing and improving productivity. The same research states that 41% of engineers spend around 4 to 6 hours per week on vendor sourcing, management, quoting, and order activities.
This highlights the need for smart automation solutions and drives the demand for RPA in supply chain management. In fact, 60% of organizations worldwide expect robotic process automation to significantly impact supply chains by 2025, according to Statista.
In addition to helping businesses overcome supply chain challenges, RPA also brings significant benefits to procurement processes. But to whom and how exactly does robotic automation bring value?
Who Benefits from Supply Chain Management RPA?
Statistics say “yes” to robotic process automation in the supply chain, and so will your employees. RPA impacts and benefits all teams involved in supply chain management, from procurement to customer service departments. And here’s how it works.
Supply chain managers
Typically, supply chain managers oversee all supply chain processes: planning, sourcing, production, and logistics. This includes many routine data analysis and reporting tasks, which can be easily automated with RPA. For example, an RPA solution can use data from various sources to generate performance reports and help managers identify bottlenecks in the process in time to address them effectively.
Logistics providers
Logistics providers coordinate the movement of products from suppliers to customers and will benefit from automated shipment tracking and documentation. RPA bots can help them by updating tracking systems in real time and notifying customers about shipment statuses. This, in turn, will reduce manual errors and improve communication.
Procurement teams
Contract negotiations and maintaining relationships with multiple logistics partners are the main responsibilities of procurement teams. RPA can automate the entire purchase order process by generating and sending purchase orders to suppliers, confirming orders, processing invoices, and tracking supplier performance.
Inventory managers
Inventory managers can easily automate inventory turnover management with an RPA system. It will track inventory levels across different locations and automatically generate alerts in low-stock or overstock cases.
Operations teams
Operations teams can also rely on RPA to improve production processes. For instance, they can use RPA to analyze production schedules and automatically adjust them based on equipment availability or workforce capacity, improving overall production efficiency.
Finance and accounting departments
Managing budgets, forecasts, financial reports, and invoices typically involves many routine tasks, such as extracting invoice data from emails, matching it with purchase orders, and processing payments. Fortunately, all of these tasks can be automated with the help of RPA.
Customer service teams
Customer service teams handle many similar inquiries and complaints, which can be time-consuming and may distract them from more serious order issues. So, to address non-complex customer inquiries, service teams can also use RPA.
Now that it’s clear RPA can benefit every member of your team, you might be wondering what your business will gain beyond high employee satisfaction. And that’s exactly what we’ll cover next.
Key Benefits of RPA in Supply Chain Management
Automating supply chains essentially provides you with an additional workforce that is more accessible, cost-effective, and can be tailored to your operational rules. This alone highlights some of the key advantages of supply chain automation. Here’s how RPA can directly benefit your business.
Reduced planning time and errors
Supply chain planning means gathering and processing large amounts of data from multiple sources, which can be quite time-consuming and prone to human errors if managed manually.
RPA bots, in turn, can quickly retrieve data from ERP systems, spreadsheets, or emails, cross-check the information, and compile it into a unified plan. All according to the rules you set.
Increased efficiency
By reducing the time a human employee would spend on hundreds of repetitive tasks, RPA allows your teams to focus on more complex tasks, which increases their overall productivity and your business's potential for growth.
Cost savings
Manual operations are expensive due to labor costs, time delays, and errors that lead to financial losses (e.g., incorrect orders or penalties for late shipments). And according to McKinsey, almost half the activities employees perform can be automated. If converted to wages, this means a potential saving of around $16 trillion.
How? Well, RPA bots can work 24/7, make fewer mistakes than human workers, and the implementation and maintenance of RPA are cost-efficient since it can be integrated into your existing system. Plus, most of the necessary adjustments can be made without an IT team.
Enhanced accuracy
As we’re sure you’re aware, errors in supply chain management are costly. That’s why businesses are striving to enhance the accuracy of task completion and data processing, and RPA is a great technology for this.
When performing tasks, the bots follow predefined rules and workflows; they can’t get distracted and can cross-check data between different systems in real time. Additionally, they can be programmed to identify anomalies or errors in the data and alert a human operator or log the error for review.
Improved customer service
Identical queries and order status updates may seem less important than bigger issues requiring in-depth investigations. But to your customers, they’re all emergencies. Trust us, they won’t think, “Oh, they probably have bigger problems; I should just wait,” when the customer support team doesn’t reply on time or forgets to inform them about shipment delays.
That’s where RPA can be handy, taking over frequently asked questions, simple queries, and status updates, improving your customer satisfaction with fast responses.
Scalability
As your business grows, you need your technology to grow with it. However, scaling traditional automation may present challenges, such as the need for system upgrades, custom code, or API extensions, which can be costly and time-consuming. In contrast, RPA can be easily scaled by increasing the number of bots or adjusting to meet new demands without involving a tech team.
And that’s how adopting robotic process automation in the supply chain can benefit your business. Now that you can clearly see the value of automation let us show you the most common RPA use cases in supply chain management.
Common Use Cases of RPA in Supply Chain
When discussing who can benefit from RPA in supply chain management, we’ve briefly mentioned the processes RPA technology automates. But to make it clearer, we’ve prepared a list of supply chain automation use cases you can use to ensure you're using RPA to the fullest.
Order processing automation
You can use RPA technology to speed up order processing by automating the entire workflow, from order receipt to order fulfillment. This includes:
- Extracting order information from emails or online forms
- Validating order details with inventory databases and price lists
- Sending order confirmations to your customers
- Updating inventory levels in real-time
- Generating reports on order status and fulfillment
With all these tasks automated, you will reduce manual intervention and ensure fewer errors in processing your customers' orders.
Inventory management
RPA can keep your inventory levels in check, saving you the time spent regularly monitoring stock. More specifically, RPA bots can help you with:
- Tracking inventory levels across multiple storage locations
- Alerting when your stock falls below a predefined amount
- Generating purchase orders for restocking
- Updating inventory records across systems in real time
- Analyzing inventory data to identify trends and optimize stock levels
Automated inventory management can minimize the risk of overstock or stockouts and help ensure that equipment or products are available when needed.
Supplier management and onboarding
Document collection, validation, and compliance checks can be pretty time-consuming when onboarding a new supplier, and performing these tasks manually might lead to costly mistakes. But you can implement RPA to handle:
- Collecting necessary documentation from new suppliers
- Validating supplier information against databases
- Checking compliance with regulatory requirements
- Updating supplier information in the management system
- Sending reminders when document updates are needed
This way, your onboarding process will be much faster and seamless, freeing up some time for you to explore better deals.
Demand planning and forecasting
For accurate demand forecasting, you normally need to collect a lot of data, go through it, extract insights, and analyze them thoroughly. But now, RPA bots can do everything for you, covering:
- Gathering historical sales data from multiple sources
- Reviewing market trends and seasonal factors and adding them to the forecast
- Generating forecast reports
- Alerting you when forecasts indicate significant changes
- Updating forecasting models based on real-time data
By using bots for demand forecasting, you can be sure that every detail and factor is considered, making the forecast more accurate.
Shipping and logistics optimization
By automating shipping requests, you can optimize routes and implement real-time tracking, which will drastically improve your logistics. RPA will help you by:
- Collecting shipping requests and routing them to appropriate carriers
- Selecting optimal shipping routes based on cost and time
- Tracking shipment status and updating stakeholders
- Generating shipping labels and documents
- Analyzing shipping data to identify areas where you can cut costs
With RPA performing all these tasks and processing the data nonstop, you can deliver faster and at a lower cost.
Invoice processing and accounts payable
Robotic process automation technology helps you reduce errors and speed up payments by automating the invoice processing and accounts payable workflow. It will help you with:
- Extracting invoice data from emails and documents
- Validating invoice details against purchase orders and receipts
- Automating approval workflows based on predefined rules
- Scheduling payments and updating accounting systems
- Generating reports on invoices and payment trends
Automation will enhance payment processing accuracy and enable finance teams to focus on more strategic tasks.
Returns management
RPA can handle your return requests, their validation, and return status updates. Essentially, it will help you by:
- Processing return requests from your customers
- Validating whether the return is eligible based on predefined criteria
- Updating inventory records upon return approval
- Sending notifications to customers about return status
- Generating reports on return trends and reasons
RPA bots will keep a finger on the pulse of your return management, leading to a better understanding of the reasons for returns and ultimately reducing their frequency.
Customer service and support
We’ve mentioned this earlier, but RPA can improve customer service by automating responses to common inquiries and providing real-time order updates. Specifically, RPA bots automate:
- Responding to frequently asked questions
- Providing personalized support based on customer data
- Routing more complex inquiries to the appropriate support team
- Updating customers on order status and shipping information
- Collecting customer feedback for further improvement
With the help of RPA, your human agents can spend more time addressing complex customer issues, increasing service quality and customer satisfaction.
After business leaders see how RPA can automate routine but essential tasks in their supply chain management, the next question is usually, “How can we adopt it?”
How to Implement RPA in Your Supply Chain?
Though considered easier than adopting traditional automation, implementing RPA in your supply chain still requires time and effort. To ensure you don’t miss anything while overseeing how your IT specialists or outsourcing vendor approach the adoption, we’ve created a list of the main stages of the process for you.
Choosing the right RPA tools
Selecting the RPA tool that matches your needs is half the battle for success. Fortunately, you have several options to choose from, and popular RPA platforms like UiPath, Automation Anywhere, and Blue Prism offer user-friendly interfaces and extensive integration capabilities. To help you choose the right tool for your organization, consider the following:
- Ensure the tool is easily scalable and can grow with your business needs.
- Check the intuitiveness of the tool's interface and opt for one that requires minimal coding knowledge.
- Choose a tool that seamlessly integrates with your existing systems.
- Select a platform that has responsive client support and an active user community.
With these tips, you can feel more confident when deciding on the RPA tool for your business.
Integration with existing systems
A smooth integration of RPA tools with your existing systems ensures that your current infrastructure and RPA bots can work more accurately and efficiently together. So, for you and your team to make it right, here are some best practices when integrating the platforms:
- It’s better to choose tools that already offer pre-built connectors or APIs compatible with your system to minimize integration challenges.
- Make sure your IT specialists develop a clear integration roadmap that outlines each step of the process with potential obstacles and aligns with your business objectives.
- To ensure that data flows seamlessly between RPA and existing systems, you can establish data governance policies that help maintain accuracy and consistency across platforms.
- There’s no need to start big; you can launch a pilot project to test the integration on a smaller scale and then scale it up.
- It’s important to equip your team with all the necessary information on how to manage and operate within the integrated systems. Ongoing training is also a good idea.
With this strategic approach to integration, you can rest assured that the process will go smoothly and eventually save you time, worry, and money.
Change management
Now, when everything is set, you need to lead your team through the transition and adaptation. To manage this effectively, you can try the approaches that worked for our clients when adapting to new technology:
- Inform your team about the benefits of RPA and how it will affect their roles and workflows (for example, you can even send them this article).
- Consider providing comprehensive training programs to help your employees understand and adapt to working with RPA.
- Create channels for your workers where they can share their experiences and suggestions regarding RPA.
- Analyze employee feedback, be attentive to your staff's reactions and concerns, and proactively help solve the challenges they face after RPA implementation.
These strategies will help ensure that your team members confidently and accurately use RPA in their work.
Monitoring and optimization
Lastly, continuously monitor and improve the performance of your tools to maximize the benefits of RPA. Here are a few key practices:
- Define key performance indicators (KPIs) to measure how effective the RPA technology is for your supply chain workflows.
- Regularly review your automated workflows to identify areas for enhancement and adapt to changing business needs.
- Use data analytics tools to understand your performance trends better and find optimization opportunities.
- Encourage your employees to seek and suggest ways to enhance RPA processes.
With all these strategies in mind, you’re now fully equipped to start your RPA implementation process. However, there is one important question left.
What Factors Impact RPA in Supply Chain Implementation Costs?
Cost is often a major factor in deciding whether to adopt a new technology. To help you better understand the financial aspect of RPA in the supply chain, here’s a breakdown of the main aspects that form the cost of its implementation:
- If your project involves multiple processes or more complex tasks, like interpreting documents or analyzing visual data, it will require more time, effort, and resources, which leads to increased expenses.
- Longer projects will naturally incur higher costs due to their extended need for development, testing, and integration.
- If your processes require bots with specialized custom configurations, the development will be more expensive compared to using out-of-the-box solutions.
- The more complex the integration with your current supply chain systems, such as ERPs or warehouse management systems, the more resources are needed to ensure platforms interact smoothly.
- If, during testing, you discover any bugs or errors that call for significant changes, the price may grow.
- Ongoing monitoring after implementation, such as bot maintenance, updates, and performance tracking, also increases operational and management expenses.
That’s what is typically included in the price of RPA implementation, and you can adjust the cost to your budget by prioritizing what features you need, how many processes you want to automate, and so on.
Conclusion
Adopting RPA in supply chain management is not just about automating routine tasks—it’s about transforming how your business operates. Now, you can empower your processes with greater accuracy while boosting your team's productivity. From streamlining inventory management to improving customer service, RPA does it all.
You might consider starting your journey to an enhanced supply chain now, or perhaps you still have a few questions that weren’t fully answered in this article. Whether it’s one or the other, you’ll likely need more detailed and personalized help to understand how RPA can be applied to your needs. That’s what ElifTech will gladly assist you with.
Our tech experts create intelligent solutions for logistics, including robotic process automation platforms to enhance supply chain management. So, if you’re ready to discuss your project, contact our team, and let’s automate your business.